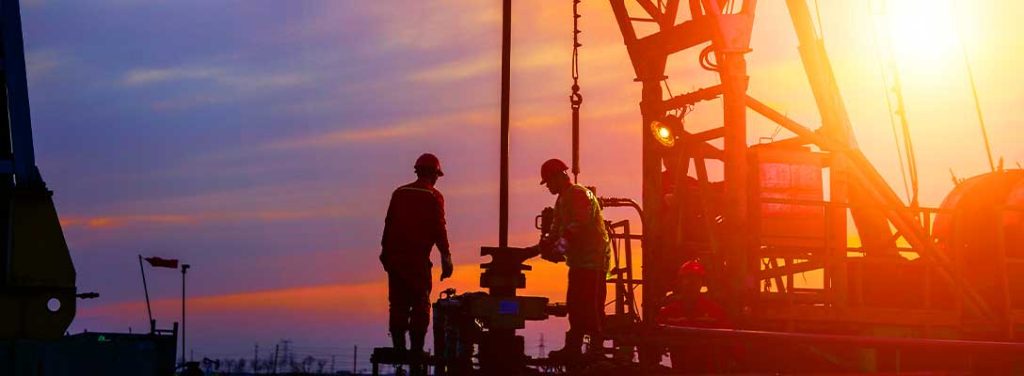
Importance of Craftsmanship in the Oil and Gas Industry
Metal Forming in the oil industry
Metal forming is used to create nearly all of the equipment and infrastructure in the oil industry. Metal forming refers to the process of shaping metals into various shapes and components such as pipes, storage tanks, drilling equipment, and offshore platform structures through processes including rolling, welding, metal spinning, stamping, and machining.
Metal fabrication is used to manufacture the infrastructure and machinery needed for oil exploration, extraction, and refining. Each of these processes require extremely durable metal applications that can withstand harsh conditions, and long-term usage.
For example, components on drilling and extracting equipment must also be made strong and durable to withstand an immense amount of force and pressure for rugged operations. Rig structures located near or in the ocean need to have applications and structural supports that are corrosion resistant and extremely durable because of salt water’s deteriorating affect on metal’s properties, and tough environmental conditions..
Metal Spinning
What are the Advantages of Metal Spinning?
At Toledo Metal Spinning Company, metal spinning has been our foundation for nearly a century. Since 1929, we have been forming metal – starting as a dedicated metal spinning company. Metal spinning offers numerous benefits, which is why we have continued perfecting our craft for nearly a century. Our skilled metal spinners have honed their craft over the past decades, passing down knowledge and expertise through generations.
CNC Technology – Extremely Efficient
Utilizing CNC technology for metal spinning and spin forming is a highly effective way to increase efficiency and cost savings. CNC metal spinning allows for automated fabrication processes for components and applications that require tight tolerances, resulting in high precision and consistency. This also allows for fast production runs with an increased number of parts.
CNC technology is extremely effective for forming basic shapes such as cones, flanged covers, hemispheres, cylindrical shells, or venturis. Minimizing tooling costs, or spinning low product volumes, CNC metal spinning is the optimal process. Pieces with complicated geometry are also easily fabricated on our cnc metal spinning lathes.
Metal Spinning allows multiple operations to be completed in a single setup with minimal downtime. As compared to other fabrication methods, it offers significantly faster setup times, reducing lead times and increasing daily production output.
Rolling and Welding Vessels
Metal cylinders, vessels, tanks, spools, accumulator housings, pipeline fittings or components, and wellhead components are rolled and welded in-house at Toledo Metal Spinning Company. What makes them special? Our skilled craftsmen combined with TIG seam welding technology and planishing makes our vessels extremely durable and ideal for industries like oil and gas.
Why is seam welding helpful for oil equipment and applications?
Seam welding is the process of joining two similar or different materials together, at the seam, by electronic current and pressure. As the current passes between the metals, heat is generated at the gap. The electrodes maintain and control the flow of electricity. The seam welding process is most common with metals, because they conduct electricity easily, and are able to sustain high pressures. Seam Welding has a great reputation for building a clear weld every time, with no filler needed.
After achieving the seam weld, we planish the weld to ensure that it is smooth all the way down the cylinder. The planishing process means that the molecules are realigned in the weld, which makes the weld much stronger and more reliable. It is possible to combine seam welding and spot welding to create gas-tight and liquid-tight joints, a necessity for certain cylindrical components. All of our custom cylinders are made with a dependable seam weld, strong and durable for oil drilling applications.
Advantages to seam welds include airtight welds, a fast weld process, no filler is required, the process can be automated, saving time and money, leaves a great reputation for providing a clear weld, and it is one of the only processes that does not emit fumes or cause any gas formation, as with other processes.
Milling and Machined Applications
Machining and Milling are ideal processes to form components and applications in the oil and gas industry because they are able to form extremely precise and accurate shapes. Metal fabricators manufacture a majority of the applications and equipment used for searching, drilling, extraction, production, and distribution phases in this industry.
Accuracy and Efficiency
Milling and CNC turning can manufacture components to exact specifications while keeping errors to a minimum and ensuring proper functionality in critical oil field and environmental operations. Equipment operating under extreme temperatures and pressures needs to be formed to be extremely durable. Reliable performance, safety, and long-lasting durability are crucial in this field of work. Some examples of durable, yet crucial pieces would be bearings, pipe fittings, pressure gauge components, drill string and bits.
Milling and machining also have the ability to manufacture one or a large batch of custom parts with ease and accuracy. The CNC technology our mill is equipped with is built to handle a multitude of parts with extreme efficiency.
Customization
Customizing parts and components to fit their exact needs is effortless and easily done to the highest of standards through milling and machining processes. CNC automated technology allows for tight tolerances and critical customizations in oil exploration, extraction, or refining equipment.